Software forOn-Demand Manufacturing
Request Consultation3YOURMIND: Addressing On-Demand Manufacturing Challenges
That's why 3YOURMIND strives to deliver on-demand solutions that address additive manufacturing challenges today while positioning companies for tomorrow's production trends.
Part Identification
Assess parts individually or en masse to identify the best technologies to produce spare parts.
Distributed Manufacturing
Turn manual part ordering and production processes into powerful digital workflows.
Part Identification: AI Software for On-Demand Manufacturing
Discover the best technologies to produce spare parts.
3YOURMIND Part Identification can analyze 2D technical drawings using artificial intelligence to help engineers quickly determine the best technology to produce parts.
Browse individual part reports to receive technology and design recommendations, compare materials, and view cost and savings estimates.
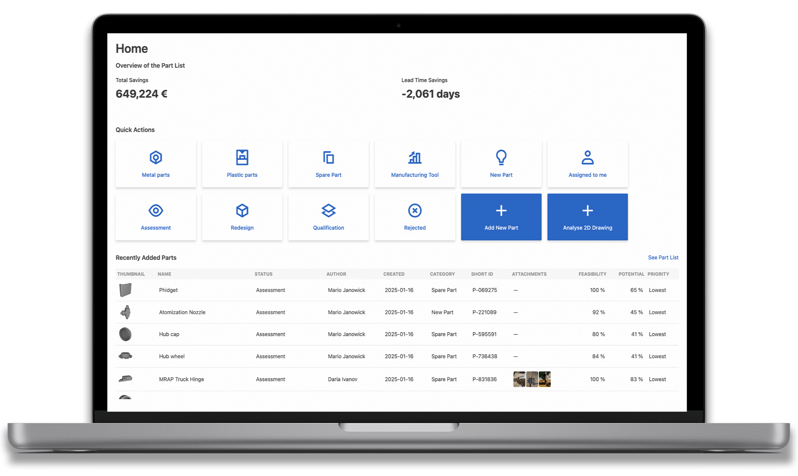
Distributed Manufacturing: Ordering and Production Software
Innovative technology requires innovative software solutions.
3YOURMIND Distributed Manufacturing is integrated order management and production software designed for service bureaus and in-house production facilities.
It implements streamlined digital workflows to support organizations in increasing revenue and scaling additive manufacturing operations.
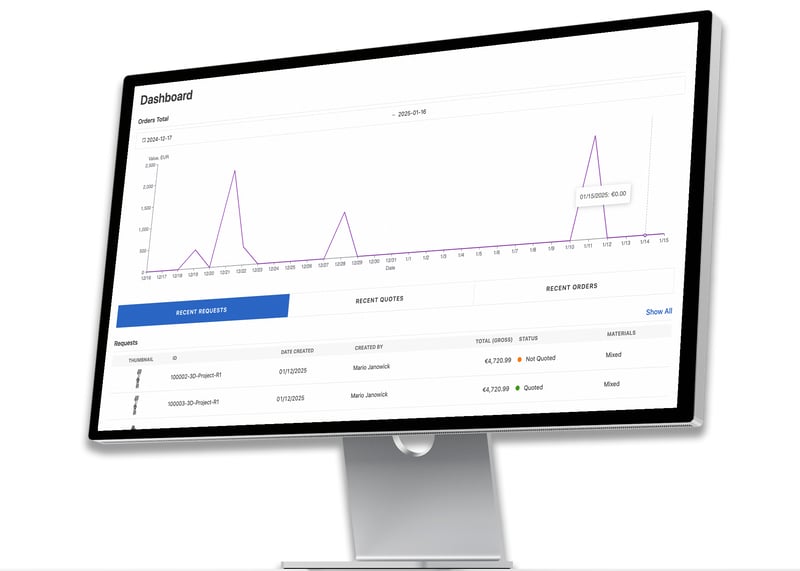
Frequently Asked Questions About 3YOURMIND
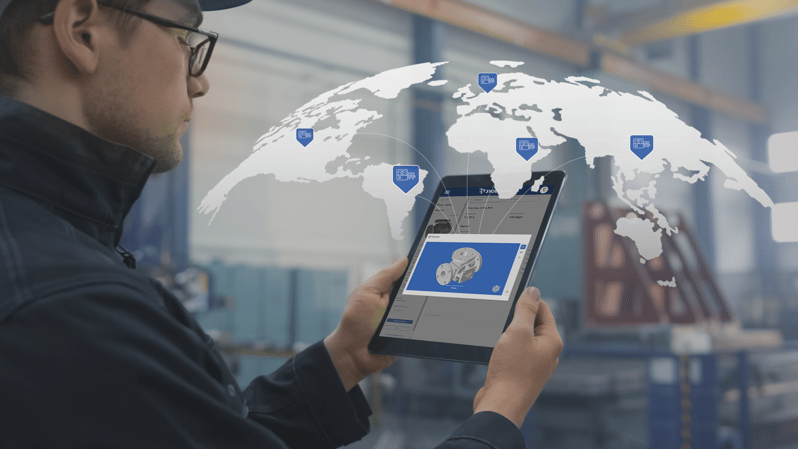
Have questions about 3YOURMIND software?
Our FAQ covers everything you need to know about 3YOURMIND's Part Identification and Distributed manufacturing solutions.
Click below to learn more about how our software can support your operations.
Browse FAQs
Let’s Stay in Touch!
Submit your e-mail address to receive news, stories, and article updates from 3YOURMIND.