Additive Manufacturing Glossary From A to Z
Get familiar with commonly used terms in additive manufacturing!
Glossary Contents:
General Terms:
- Additive Manufacturing
- Build Orientation
- Design for Additive Manufacturing (DfAM)
- Digital Inventory
- Digital Warehouse
- Distributed Production
- Injection Molding
- Just In Time (JIT) Manufacturing
- Metal Additive Manufacturing
- On-Demand Manufacturing
- Subtractive Manufacturing
- Technical Drawings
Additive Manufacturing Materials:
Additive Manufacturing Technologies:
- Binder Jetting
- Direct Metal Laser Sintering
- Electron Beam Melting
- Fused Deposition Modeling
- Powder Bed Fusion
- Selective Laser Melting
- Selective Laser Sintering
- Wire Arc Additive Manufacturing
Additive Manufacturing
Additive manufacturing, also known as 3D printing, is a manufacturing process that builds objects layer by layer using digital 3D models. Unlike traditional subtractive manufacturing methods, such as machining or cutting materials to create a final product, additive manufacturing adds material to construct an object. This process allows for more complex and intricate designs, reduces waste, and enables the production of customized or small-batch items with relative ease.
Applications of 3D printing span various industries, including aerospace, healthcare, automotive, consumer goods, and more. It has revolutionized product development, prototyping, and manufacturing processes by offering greater design freedom, faster production cycles, and new possibilities for innovation. As the technology continues to evolve, its impact on manufacturing and product development is likely to expand further.
Binder Jetting
Binder Jetting is an additive manufacturing (AM) or 3D printing technology that selectively deposits a liquid binding agent onto a powdered material layer, binding the particles together to create a solid object. This process is particularly notable for its speed and its ability to produce complex and large parts, making it suitable for various applications.
Binder Jetting is known for its ability to produce parts quickly and cost-effectively, especially for applications where high accuracy and precision are not the primary requirements. It is commonly used in industries such as automotive, aerospace, and tooling for prototyping, production of sand molds for casting, and creating intricate parts that might be challenging with other manufacturing methods. The technology is suitable for a range of materials, including metals, ceramics, and composites.
Build Orientation
Build orientation in additive manufacturing (AM) refers to the specific orientation in which a 3D model or part is positioned during the printing process. The chosen build orientation can have a significant impact on various aspects of the printed object, including its structural integrity, surface finish, support structure requirements, and overall printing efficiency.
Optimizing build orientation is an essential part of the design and pre-processing phase in additive manufacturing. Designers and engineers often use software tools to analyze and adjust build orientation to achieve the desired balance between structural integrity, surface quality, and printing efficiency for a specific application.
Ceramic Materials
Ceramic materials refer to materials composed of inorganic compounds, typically non-metallic, that exhibit properties such as high-temperature resistance, hardness, wear resistance, and electrical insulation. Ceramic additive manufacturing involves the layer-by-layer deposition or solidification of ceramic materials to create three-dimensional objects with complex geometries.
Ceramic additive manufacturing is utilized in various industries, including aerospace, automotive, healthcare, electronics, and energy. The ability to produce intricate and customized ceramic components with complex geometries makes it valuable for applications where traditional manufacturing methods may be limited.
Common ceramic materials used in additive manufacturing include:
Alumina (Al2O3): Alumina ceramics are known for their high hardness, wear resistance, and electrical insulating properties. They are used in applications such as cutting tools, bearings, and insulators.
Zirconia (ZrO2): Zirconia ceramics exhibit high strength, toughness, and resistance to wear. They are often used in dental applications, medical implants, and components for machinery.
Silicon Carbide (SiC): Silicon carbide ceramics are known for their excellent thermal conductivity, high-temperature stability, and hardness. They find applications in the aerospace industry, electronic components, and high-performance machinery.
Aluminum Oxide-Titanium Carbide (Al2O3-TiC) Composites: These composites combine the hardness of aluminum oxide with the toughness of titanium carbide. They are used in cutting tools and wear-resistant components.
Silicon Nitride (Si3N4): Silicon nitride ceramics offer high strength, thermal shock resistance, and low thermal expansion. They are used in ball bearings, cutting tools, and automotive components.
Lithium Aluminate (LiAlO2): Lithium aluminate ceramics are known for their excellent thermal conductivity and are used in applications such as heat exchangers.
Composite Materials
Composite materials in additive manufacturing (AM) are composed of two or more distinct components with different properties combined to create a material with improved performance or characteristics. In the context of additive manufacturing, composites are used to enhance specific features of 3D-printed objects, such as strength, stiffness, or thermal conductivity.
In additive manufacturing, composite materials are often used with specific printing technologies to create objects with tailored properties. For example, composite filaments with reinforcing fibers can be used in fused deposition modeling (FDM) printers. In contrast, composite powders can be employed in powder bed fusion (PBF) processes such as selective laser sintering (SLS) or selective laser melting (SLM).
Common types of composite materials in additive manufacturing include:
Carbon Fiber Reinforced Polymers (CFRP): In CFRP composites, carbon fibers are embedded in a polymer matrix. These composites are known for their high strength-to-weight ratio, stiffness, and impact resistance. Carbon fiber composites are used in aerospace, automotive, sports equipment, and other applications where strength and lightness are critical.
Glass Fiber Reinforced Polymers (GFRP): Similar to CFRP, GFRP composites consist of glass fibers embedded in a polymer matrix. Compared to other materials, these composites provide improved strength, impact resistance, and cost-effectiveness. GFRP is used in various industries, including automotive, consumer goods, and construction.
Metal Matrix Composites (MMCs): In MMCs, reinforcing materials such as ceramic particles or fibers are incorporated into a metal matrix. These composites offer enhanced mechanical and thermal properties. Metal matrix composites are used in aerospace, automotive, and electronic applications.
Ceramic Matrix Composites (CMCs): CMCs consist of ceramic fibers or particles embedded in a ceramic matrix. These composites exhibit high-temperature resistance, wear resistance, and lightweight properties. CMCs find applications in aerospace, energy, and high-performance machinery.
Polymer Matrix Composites (PMCs): PMCs consist of reinforcing fibers or particles embedded in a polymer matrix. These composites offer a good balance of strength, flexibility, and cost-effectiveness. They are commonly used in automotive components, consumer goods, and various industrial applications.
Design for Additive Manufacturing (DfAM)
Design for Additive Manufacturing (DfAM) is an approach that focuses on optimizing the design of a product specifically for additive manufacturing processes. It involves considering the unique capabilities and constraints of additive manufacturing technologies to create designs that take full advantage of the benefits offered by these processes.
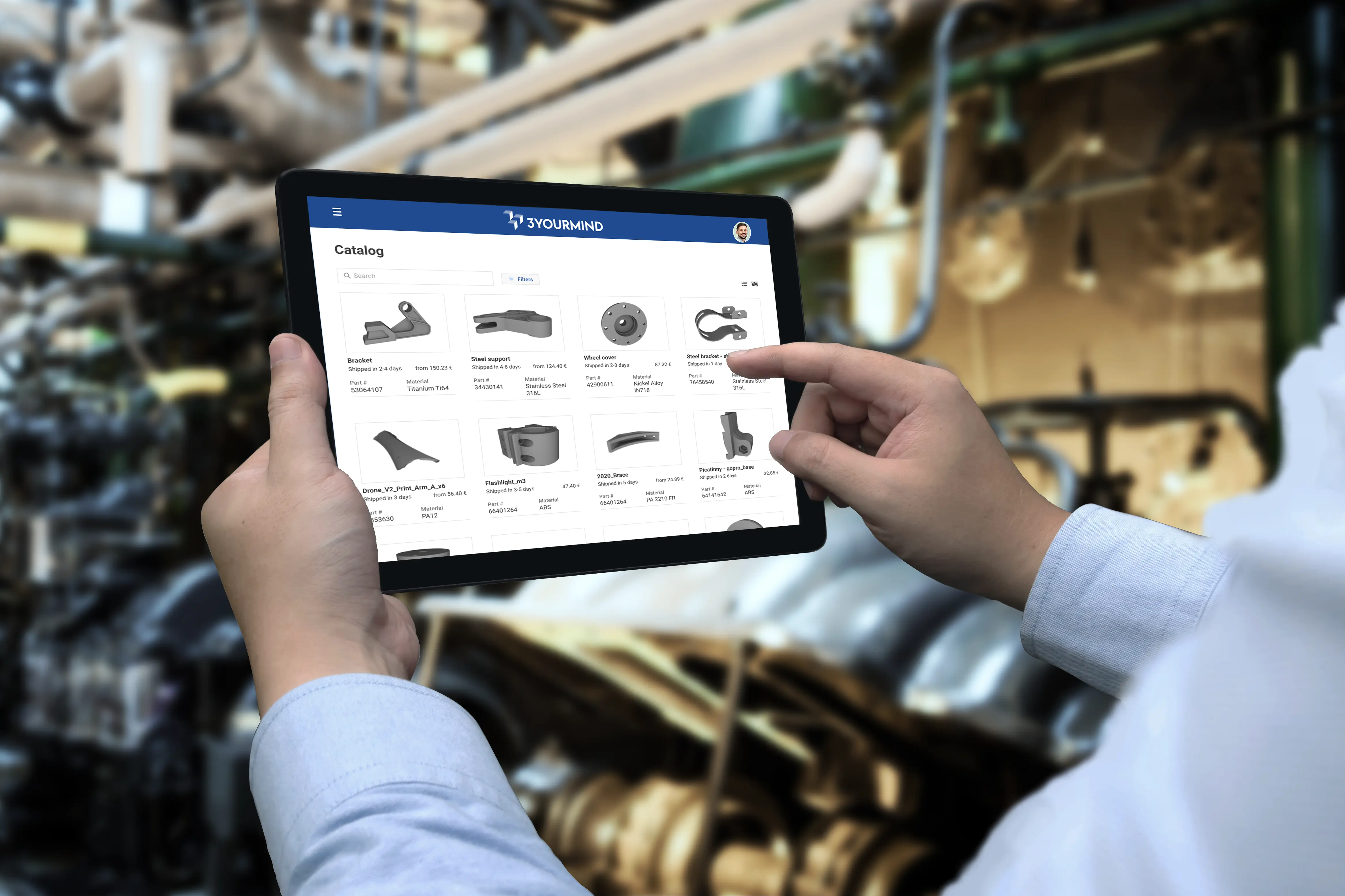
Digital Inventory
In the context of additive manufacturing (AM) or 3D printing, the term "digital inventory" refers to a digital repository or database of 3D models and design files rather than a physical stock of finished goods. This concept aligns with the idea that additive manufacturing enables on-demand and decentralized production, creating products directly from digital files without the need for traditional inventory storage.
Digital Warehouse
In additive manufacturing, "digital warehouse" refers to a virtual or digital representation of the various digital assets and resources associated with additive manufacturing processes. This includes not only the 3D models and design files, and other digital information and tools relevant to the additive manufacturing workflow. The concept of a digital warehouse aligns with the broader digitalization trend in manufacturing and supply chain management.
Direct Metal Laser Sintering
Direct Metal Laser Sintering (DMLS) is an additive manufacturing (AM) or 3D printing technology that uses a high-powered laser to selectively sinter metal powders, layer by layer, to create fully dense three-dimensional metal parts. DMLS is a specific type of metal additive manufacturing that falls under the powder bed fusion category.
Direct Metal Laser Sintering is particularly well-suited for producing complex and intricate metal parts with high precision. It allows for the fabrication of functional metal components with features that may be challenging or impossible to achieve using traditional manufacturing methods. DMLS is commonly used in industries such as aerospace, automotive, healthcare, and tooling, where the production of high-performance metal parts is crucial. The technology supports a variety of metal materials, including stainless steel, titanium, aluminum, and nickel alloys.
Distributed Production
Distributed production refers to a manufacturing model in which the production process is decentralized and dispersed across multiple locations or facilities, often geographically distributed. Instead of relying on a single centralized production facility, distributed production involves using various smaller production units or facilities located in different regions or even countries.
Elastomer Materials (Rubbers)
Elastomers, referred to as rubbers, are a class of polymers known for their elasticity and flexibility. These materials can undergo significant deformation and then return to their original shape. Elastomers in additive manufacturing are employed in various industries, including consumer goods, automotive, healthcare, and industrial applications. The ability to 3D print flexible and rubber-like components allows for creating prototypes, gaskets, seals, and other parts that require elasticity and deformability.
Common elastomers used in additive manufacturing include:
Thermoplastic Polyurethane (TPU): TPU is a versatile elastomer with excellent flexibility, durability, and abrasion resistance. It is commonly used for producing flexible prototypes, gaskets, seals, and other applications where elasticity is essential.
Thermoplastic Elastomers (TPE): TPEs are a class of polymers that combine the characteristics of rubber with the processing advantages of thermoplastics. They are used for applications requiring both flexibility and ease of processing, such as soft-touch grips and seals.
Nitrile Rubber (NBR): NBR is known for its oil and fuel resistance, making it suitable for applications such as gaskets and seals in the automotive industry.
Silicone Rubber: Silicone rubbers offer excellent heat resistance, electrical insulation, and biocompatibility. They are used in various applications, including medical devices, kitchenware, and automotive components.
Fluoroelastomers (Viton): Fluoroelastomers are known for their exceptional chemical resistance, high-temperature stability, and resistance to fuels and oils. They find applications in seals, gaskets, and other components in harsh environments.
Electron Beam Melting
Electron Beam Melting (EBM) is an additive manufacturing (AM) or 3D printing technology that belongs to the Powder Bed Fusion (PBF) category. In EBM, a focused electron beam is used to selectively melt and fuse metal powders layer by layer, creating fully dense three-dimensional objects. This process is particularly suited for producing high-quality metal parts with complex geometries.
Electron Beam Melting is known for its ability to produce fully dense and high-strength metal parts with excellent material properties. It is commonly used in aerospace, healthcare, and automotive industries, where the production of complex metal components with superior mechanical characteristics is essential. EBM allows for creating parts that meet stringent industry standards and specifications.
Fused Deposition Modeling (FDM)
Fused Deposition Modeling (FDM) is an additive manufacturing technology in the category of 3D printing processes. It is a widely used and accessible method for creating three-dimensional objects layer by layer. FDM is known for its simplicity, cost-effectiveness, and versatility. FDM employs a thermoplastic filament, typically in the form of a spool, as the build material. Common filaments include acrylonitrile butadiene styrene (ABS) and polylactic acid (PLA).
FDM employs a thermoplastic filament, typically in the form of a spool, as the build material. Common filaments include acrylonitrile butadiene styrene (ABS) and polylactic acid (PLA). Fused Deposition Modeling is commonly used for rapid prototyping, design validation, and the production of concept models. It is widely utilized in various industries, including aerospace, automotive, healthcare, and consumer goods. FDM 3D printers are famous for their ease of use, affordability, and ability to handle a wide range of thermoplastic materials, allowing for diverse applications.
Injection Molding
Injection molding is a traditional manufacturing process for producing parts by injecting molten material into a mold. It is one of the most common methods for manufacturing plastic parts, and it is widely used for producing various products ranging from small components to larger objects.
Injection molding is known for its efficiency, repeatability, and ability to produce complex shapes with high precision. It is widely used in various industries, including automotive, electronics, medical devices, consumer goods, etc. The versatility of injection molding makes it a preferred method for economically producing a diverse range of plastic parts.
Just in Time (JIT) Manufacturing
Just In Time (JIT) Manufacturing is a production strategy aimed at producing goods at the exact time they are needed in the production process or by the customer, minimizing the need for inventory and associated holding costs. The goal of JIT is to improve efficiency, reduce waste, and enhance overall productivity in the manufacturing process.
JIT manufacturing is widely used in industries such as automotive, electronics, and consumer goods, where efficiency, responsiveness, and cost-effectiveness are critical factors. While JIT offers significant benefits, it also requires careful planning and effective coordination throughout the supply chain to minimize the risks associated with potential disruptions.
Metal Additive Manufacturing
Metal additive manufacturing (AM), also known as metal 3D printing, refers to a group of technologies that produce three-dimensional objects by selectively adding material layer by layer. In the context of metal additive manufacturing, these layers are typically composed of metal powders or wire feedstock. The process allows for the creation of complex and intricate metal components with high precision.
Various metal additive manufacturing technologies exist, and they differ in terms of the specific methods used to add and fuse the metal material. Some of the common metal AM processes include SLM, EBM, DMLS, Binder Jetting, and Metal Material Extrusion.
Metal Materials
Metal materials refer to a class of materials used to create three-dimensional objects by selectively adding or fusing metal powder or wire layer by layer. Metal additive manufacturing technologies allow for the production of complex and intricate metal components with high precision. These technologies are utilized in various industries, including aerospace, automotive, healthcare, and tooling.
Common metal materials used in additive manufacturing include:
Stainless Steel: Offers good corrosion resistance, strength, and ductility. Commonly used for a wide range of applications, including tooling and functional prototypes.
Aluminum: Known for its low density and good strength-to-weight ratio and used in aerospace, automotive, and other applications where lightweight structures are desirable.
Titanium: Offers high strength, corrosion resistance, and biocompatibility. Widely used in aerospace, medical implants, and other demanding applications.
Inconel: High-temperature and corrosion-resistant material. Used in aerospace, automotive, and oil and gas industries for parts subjected to extreme conditions.
Cobalt-Chrome Alloys: Known for their high strength, corrosion resistance, and biocompatibility, they are used in medical and dental applications, as well as aerospace.
Tool Steel: Includes various steel alloys designed for tool and die applications. Used in tooling and molds.
Precious Metals (Gold, Silver, Platinum): Used for specialized applications, such as jewelry, dental components, and high-value parts.
On-Demand Manufacturing
On-demand manufacturing refers to a production model where goods are produced in response to customer orders or demand rather than being manufactured in anticipation of future orders or maintaining a large inventory of finished goods. This model is characterized by its flexibility, allowing companies to produce items quickly and efficiently based on current market demand.
Polymer Materials
Polymer materials refer to a class of materials that are used to create three-dimensional objects through layer-by-layer deposition or solidification processes. These materials are in a polymer state (plastic or resin) during printing and are solidified or cured to form the final object. Polymer-based additive manufacturing is widely used for prototyping, product development, and the production of functional parts in various industries.
Examples of widely used polymer materials:ABS (Acrylonitrile Butadiene Styrene): Known for its strength, impact resistance, and durability and commonly used for prototyping and functional parts.
PLA (Polylactic Acid): A biodegradable and environmentally friendly material. Often used for prototyping, educational purposes, and consumer products.
PETG (Polyethylene Terephthalate Glycol): Combines the strength of ABS with the ease of printing of PLA. Suitable for functional parts.
Nylon: Offers high strength, flexibility, and chemical resistance. Used for a variety of applications, including engineering prototypes.
TPU (Thermoplastic Polyurethane): Known for its flexibility and elasticity and used for flexible prototypes and parts requiring impact resistance.
Polypropylene: Known for its chemical resistance and flexibility and used in applications requiring these properties, such as packaging and containers.
Powder Bed Fusion (PBF)
Powder Bed Fusion (PBF) is a category of additive manufacturing (AM) processes that involve selectively fusing or melting powdered material to build three-dimensional objects layer by layer. In PBF, a thin layer of powdered material is spread across a build platform, and each layer is selectively fused using a heat source (such as a laser or electron beam) based on a digital model's specifications.
Powder Bed Fusion processes are known for their ability to produce complex, high-quality parts with excellent material properties. They are widely used in industries such as aerospace, automotive, healthcare, and more, especially when working with metals or high-performance polymers.
Selective Laser Melting (SLM)
Selective Laser Melting (SLM) is an additive manufacturing or 3D printing technology that falls under the Powder Bed Fusion (PBF) category. In SLM, a high-powered laser selectively melts and fuses metal powders layer by layer to create three-dimensional objects. This process is particularly notable for its ability to produce fully dense metal parts with complex geometries.
Selective Laser Melting is known for its ability to produce fully functional and complex metal parts directly from digital models. It is utilized in various industries, including aerospace, healthcare, automotive, and manufacturing, where the production of high-performance metal components with intricate geometries is critical. The technology allows for the creation of parts that may be challenging or impossible to produce using traditional manufacturing methods.
Selective Laser Sintering (SLS)
Selective Laser Sintering (SLS) is an additive manufacturing or 3D printing technology that uses a laser to selectively sinter or fuse powdered material layer by layer to create three-dimensional objects. This process belongs to the powder bed fusion category of additive manufacturing.
Selective Laser Sintering offers several advantages:
- Material Versatility: SLS can work with various materials, including polymers (plastics) and, in some cases, metal powders.
- Complex Geometries: SLS is capable of producing complex and intricate geometries, including parts with internal structures and moving components.
- No Need for Support Structures: The surrounding powder acts as a natural support during the printing process, reducing the need for additional support structures for overhanging features.
- Batch Production: SLS can be used for batch production, producing multiple parts simultaneously within the same build chamber.
Subtractive Manufacturing
Subtractive manufacturing is a traditional manufacturing process that involves removing material from a workpiece to achieve the desired shape, size, and features. Unlike additive manufacturing, which builds objects layer by layer, subtractive manufacturing starts with a block or material. It removes excess material through machining, cutting, or other processes to create the final product.
Common subtractive manufacturing processes include milling, turning, drilling, grinding, and laser cutting. These processes are utilized in various industries, such as aerospace, automotive, medical, and consumer goods, to produce various components and products.
Technical Drawings
Technical drawings, also known as engineering drawings or blueprints, are graphical representations of an object or system used by engineers, architects, and other professionals in the design and manufacturing industries. These drawings provide detailed information about the size, shape, materials, and specifications of a product or structure. Technical drawings serve as a universal language allowing individuals to accurately and precisely communicate complex information.
Technical drawings are created using Computer-Aided Design (CAD) software or can be hand-drawn in traditional drafting. The adoption of CAD has significantly improved the efficiency and accuracy of technical drawings, allowing for easier revisions, digital storage, and the integration of 3D models.
Wire Arc Additive Manufacturing (WAAM)
The term "wire arc" typically refers to a welding process known as gas metal arc welding (GMAW) or metal inert gas (MIG) welding. In this welding method, a wire electrode is continuously fed from a spool through a welding gun, and an electric arc is established between the wire and the workpiece. The heat generated by the arc melts the wire, and the molten metal is transferred to the workpiece, creating a weld.
Wire arc welding is widely used in various industries for its versatility, efficiency, and ability to weld different materials and thicknesses. It is commonly employed in manufacturing, construction, automotive, and repair applications. The process is relatively fast and can be automated, making it suitable for both manual and robotic welding setups.