Case Study: U.S. Marine Corps. Identifies Part for AM
In this case study, learn how the United States Marine Corps leverages software to organize technical data and identify part candidates for additive manufacturing.
Originally published on advancedmanufacturing.org.
Vision:
The United States Marine Corps. (USMC) is going ‘all in’ on additive manufacturing.
Additive manufacturing (AM), commonly called 3D printing, is often touted for its implications as a solution to replace traditional equipment sustainment supply chains. In theory, additive manufacturing enables equipment operators to produce parts at the point of need.
Still, today, few organizations are moving the needle to turn the idea from dream to reality. The USMC’s Advanced Manufacturing Systems Team (AMS) seeks to change that.
“The Marine Corps. is very focused on pushing [additive manufacturing] as far forward as we possibly can to the point of need,” says Douglas McCue, AM Program Analyst at AMS.
Today, the USMC already has several programs of record for additive manufacturing that are being pushed out to fleet forces.
However, it doesn’t end there. Currently, the Marine Corps. is laying the groundwork for three fabrication capabilities that can be deployed at or near the point of use: expeditionary fabrication (or XFAB) will equip expeditionary units with industrial-level polymer systems; tactical fabrication kits (TacFab Kits) a smaller capability than the XFAB but will be sent to every unit in the Marine Corps enable the warfighter to use an industrial-level printer to build parts wherever deployed or stationed; as well as a third, more established or semi-permanent fabrication centers located in Marine Corps garrisons and depots.
Get the Highlights: Download the Case Study
“If we already have a repository full of AM candidates, then Marines can readily access part files, print them, and put them on equipment,” says McCue. “We’re not trying to replace our supply system; we’re trying to augment it for parts we just don’t have on hand.”
McCue says the Marine Corps primarily focuses on repair parts and consumables, colloquially known as the Digital Class 9 Block.
“The more stuff we can take out of Class 9, the less of the Iron Mountain we have to bring with us,” says McCue.
Sgt. Douglas McCue – photo by Gunnery Sgt. Jason W. Fudge
Challenge:
The USMC has grand ambitions for its advanced manufacturing initiatives, but bringing them to fruition requires reconciling existing operational systems and adapting them for modernized use. Thus far, the branch’s additive manufacturing efforts have largely been initiated by the work of individuals.
“As the Marine Corps., we've been very grassroots with additive manufacturing,“ says McCue.” We relied heavily on our fleet Marines and everyone else to identify problems and push them up to us.”
Although McCue says that USMC has successfully developed additive manufacturing use cases due to the enthusiasm and ingenuity of select Marines, the department understands that a program must be implemented from the top down to scale additive manufacturing across the branch.
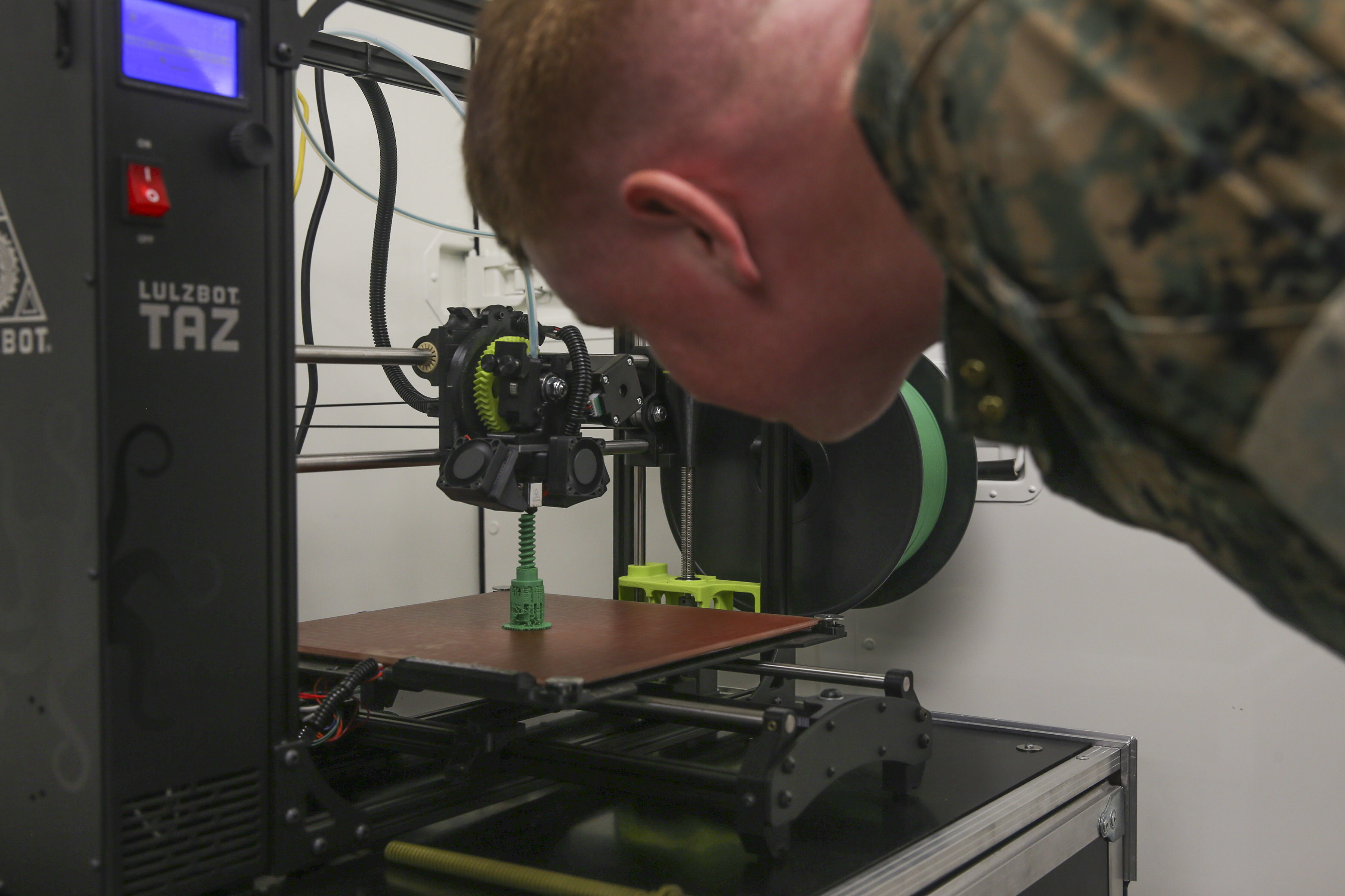
Cpl. Jade M. Pittman observes a 3D print job on a desktop 3D printer. Photo by Lance Cpl Tyler Stewart
One of the challenges the AMS had to contend with was the question of data. The USMC has no shortage of parts to evaluate for additive manufacturing. However, the data was largely unstandardized. Many parts often didn’t have files; some merely had data points distributed across multiple locations and departments, making it challenging for USMC engineers to begin examining and reverse engineering parts to produce with advanced manufacturing methods.
To address this, the USMC is developing a Digital Manufacturing Data Vault (DMDV), which functions as a repository for Marines to upload part data that they have reverse-engineered or look for parts that engineers from other departments have already developed and are already qualified for production.
But having a digital repository to hold data wasn’t enough; they needed a software solution to read the data, standardize it, and provide recommendations for what parts engineers should explore first.
That’s when the USMC began working with 3YOURMIND.
Solution:
The USMC already had established relationships with Phillips Corporation Federal Division, an additive manufacturing equipment reseller, and long-term government contractor, to configure additive manufacturing machines that support the Department of Defense’s specific and often complicated hardware requirements. Phillips Corps. supports and configures the USMC’s arsenal of Advanced Manufacturing Technologies and introduced 3YOURMIND as the selected additive manufacturing software vendor for Operation Trailblazer, a multi-year program to enhance the USMC’s additive manufacturing capabilities.
One of those capabilities was to prove that software could help streamline additive manufacturing part identification for the USMC on a broader scale. According to William Cuervo, 3YOURMIND’s VP of Sales North America and a close collaborator on the project, the software allows the USMC to interpret data from multiple sources and in different states of completeness to find a common thread.
“Using standard, manual methods, it can take experts a significant amount of time to analyze a part from a process perspective,” says Cuervo.
To evaluate just one part, experts may have to pull data from different databases, centralize it, build formulas in a spreadsheet, and then analyze it, which can be a slow and arduous process, says Cuervo.
“That’s just one part,” says Cuervo. “Now imagine having to repeat that process dozens, if not hundreds of times to address requests from personnel with a critical need for parts.”
According to McCue, gathering data from different departments in different formats was one of the most challenging aspects, but the exercise brought powerful realizations to the surface.
“We wanted to run our data through the 3YOURMIND software to identify AM candidates,” says McCue, “Although we ran into a few issues being able to get a lot of the data, it opened our eyes to AM candidate software tools out there.”
Results:
Once McCue and his team at AMS understood what data they needed to identify AM candidates, progress came quickly.
“We pushed through about 10,000 line items [through the 3YOURMIND software], which was super impressive,” says McCue. “And what was interesting is that we didn’t have to have technical data for all of those 10,000 items to do that.”
The team used several data formats to examine AM candidates with 3YOURMIND software, including more complete assets like 3D CAD models and prints, to bare-bones data points like the cost of traditional parts or the annual demand quantity.
“We were able to take a lot of that incomplete data and pull AM candidates,” says McCue. “Even though we may not have had all the technical data info, we could still get results out of it and go back and deep dive on some of the most likely AM candidates, which was awesome.”
Examples of 3D printed part candidates identified by Advanced Manufacturing Systems
Out of the first 10,000 parts analyzed, AMOC found 300+ parts with AM potential. From that quantity, McCue and his team of engineers have prioritized 30 strong AM candidates that are being tested and qualified for AM.
The parts with strong AM potential had to score high in financial and technical feasibility. In other words, whether a given part made financial sense to produce with additive manufacturing and whether the part satisfied the technical requirements needed to produce it.
The analysis identified several part types that satisfied the requirements in both categories, including plugs, covers, gaskets, and covers. In the financial and technical categories, 50% and 64% were identified as potential metal parts, respectively.
“Since Marines have to reverse engineer parts, identifying those part candidates was a way that we could automate the process,” says McCue. “We can go through and feed data for particular capabilities, particular weapon systems, and identify candidates from that and provide our program offices and managers something to really look into and build out those particular parts.”
Ultimately, AMS’s mission is to find solutions for Marines who need parts.
What’s Next:
Merely identifying parts that are strong AM use cases is not where the journey ends for the USMC, however. In July 2023, the USMC kicked off year two of Operation Trailblazer, which aims to test and prove AM capabilities in the real world.
“In the second year, we really want to prove how AM can be done,” says McCue. “We’re going to push these parts out, print them, and put those parts on actual equipment.”
The USMC isn’t backing down from the challenge and intends to go head-first into producing metal AM parts that Marines can test – a notoriously difficult process. Once the parts are re-engineered, certified, and tested on real equipment, they will be submitted to the DMDV so that other Marines stationed anywhere in the world can select a part and produce it at their nearest print location.
“This year is really about proving that not only can we identify AM candidates, we can follow through on the whole process and build the whole part,” says McCue.
Get the highlights: Download the USMC Case Study