We Help Critical Industries Scale On-Demand Manufacturing
Our company supports critical industries like oil and gas, transportation, and defense to scale on-demand manufacturing by addressing problems like unexpected downtime, high maintenance costs, and limited parts availability.
3YOURMIND's Part Identification software equips MROs and government enterprises with an intelligent solution to identify on-demand manufacturing use cases, enabling part-production on demand. As a result, enterprises can reduce reliance on physical warehouses and ensure efficient operations.
3YOURMIND's Distributed Manufacturing software is well-suited for OEMS that want to create a catalog of digital spare parts that can be shared with in-house production facilities or produced with external suppliers, like contract manufacturers.
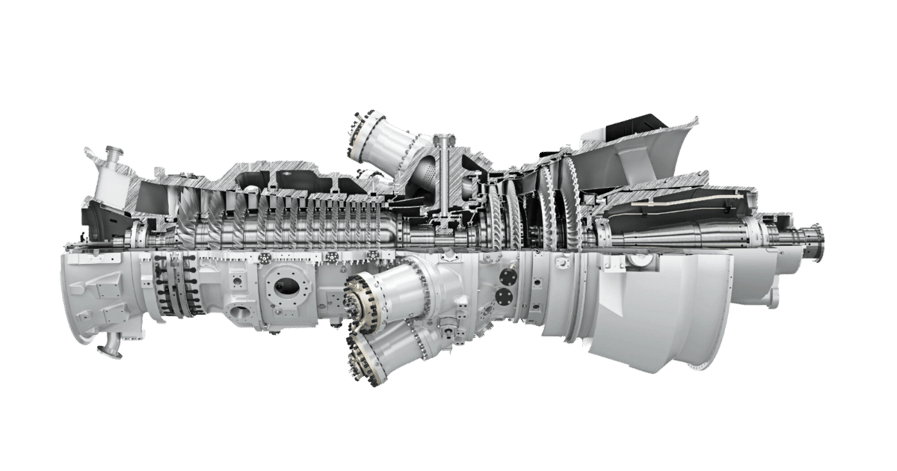
3YOURMIND's Industry Expertise
Defense & Aerospace
Defense & Aerospace
Energy
Energy
Transportation & Railway
Transportation & Railway
Discover Why Customers Choose 3YOURMIND
At 3YOURMIND, we help customers develop sustainable, scalable on-demand manufacturing capabilities.
Our Approach:
- Step-by-step guidance: We work closely with you to ensure successful implementation.
- Quick ROI: Experience fast returns with our 'lighthouse' approach.
- Top-notch security: Our software meets the highest industry standards for cloud and on-premise security.
- Seamless integration: Connect hardware and software using our open APIs for data continuity and traceability.
Don't See Your Industry? We Can Help!
Contact us to discuss how 3YOURMIND's scalable software solutions can benefit your organization's operations.
Let's ChatLet’s Stay in Touch!
Submit your e-mail address to receive news, stories, and article updates from 3YOURMIND.